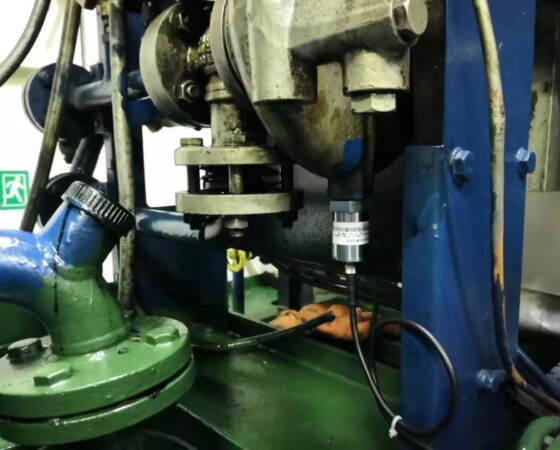
A moisture in oil sensor, also known as a moisture content sensor or water content sensor, is important in various industries, particularly those involving the use of oils and lubricants, for several reasons:
- Equipment Reliability and Longevity: Moisture in oil can be detrimental to the performance and lifespan of machinery and equipment. Water can cause corrosion, wear, and lubrication breakdown, leading to premature equipment failure. A moisture in oil sensor helps maintain the desired oil quality, preventing equipment damage and extending its service life.
- Lubrication Effectiveness: Moisture in oil can dilute and degrade the lubricating properties of the oil. Adequate lubrication is crucial for minimizing friction, reducing heat, and preventing mechanical wear in moving parts. Monitoring moisture content ensures that the oil remains effective as a lubricant.
- Early Detection of Leaks or Contamination: An increase in moisture content in oil can signal potential issues, such as leaks in seals or gaskets, or contamination of the oil with external water sources. Detecting these problems early allows for proactive maintenance and the prevention of more significant equipment failures.
- Environmental and Safety Considerations: Certain applications, such as power transformers, hydraulic systems, or gearboxes, require strict control of moisture levels in the oil. High moisture content can lead to electrical issues in transformers and combustion problems in hydraulic systems. It’s critical to maintain safe operating conditions and environmental compliance.
- Process Efficiency: In industrial processes, moisture in oil can negatively affect the efficiency and consistency of operations. This is particularly relevant in sectors like food and beverage, pharmaceuticals, and chemicals, where product quality and consistency are paramount. Maintaining low moisture levels in oil ensures the quality and integrity of the end product.
- Predictive Maintenance: Monitoring moisture in oil is a part of predictive maintenance strategies. By tracking changes in moisture levels over time, maintenance personnel can predict when equipment might need servicing or when oil needs replacement, reducing unplanned downtime and optimizing maintenance schedules.
- Cost Savings: Early detection of moisture-related issues and maintenance needs can result in cost savings. Preventing equipment breakdowns and reducing the frequency of oil changes can lead to lower maintenance and operational costs.
- Regulatory Compliance: In some industries, there are strict regulatory requirements for monitoring and controlling moisture levels in oils and lubricants. Compliance with these regulations is essential to avoid penalties and maintain industry standards.
In summary, a moisture in oil sensor like the Kongter KT-200 Moisture Transmitter is very important for maintaining equipment reliability, performance, and safety. It allows for early detection of moisture-related issues, supports predictive maintenance, and contributes to cost savings while ensuring compliance with industry regulations.